Polished Concrete Floor Types
Polished concrete floors have become synonymous with modern luxury. Over the past decade, they’ve emerged as one of the most popular flooring solutions for residential and commercial construction. A key attraction of polished concrete floors is the wide variety of achievable finishes. In new construction, architects and designers specify various aspects of concrete floors, including the concrete mix, troweling of the new slab, and the grinding, finishing, and polishing processes after curing. This article provides an overview of these decisions. If you need assistance in achieving the perfect finish for your project, contact us for a free consultation.
What are Polished Concrete Floors?
Polished concrete floors are a popular flooring option known for their durability, modern aesthetic, and low maintenance. The installation process involves grinding a concrete slab with diamond grinding tools, starting with aggressive tools for initial “cutting” steps. These steps remove imperfections, flatten the surface, and homogenize its appearance. Depending on the concrete mix and pour quality, as well as the desired finish, multiple cutting steps may be required to expose the desired stone aggregate within the concrete. This exposed aggregate can enhance the visual appeal of the floor.
After the cutting phase, the process transitions to the polishing steps, where finer diamond tools are used to refine the surface. These steps progressively increase the floor’s reflectivity, resulting in a satin or glossy finish, depending on the desired level of shine. The number of polishing steps determines the final reflectivity, with more steps yielding a more reflective surface. Polished concrete floors are valued for their versatility, as they can be tailored to suit various design preferences and functional requirements. This combination of aesthetics and practicality makes them a sought-after choice for both residential and commercial spaces.
Want to Learn More About Polished Concrete Floors?
We’re here to guide you through the design of our products. A Concrete Floor Specialist will reach out within one business day.
Aggregate Exposure Levels
Cream Polished Concrete
Cream-polished concrete floors are a popular choice for their organic, natural aesthetic and smooth, seamless finish. Unlike other polished concrete styles, cream polish skips the aggressive “cutting” steps, preserving the original surface of the concrete pour. This process leaves the subtle, natural variations from the pour intact, resulting in a unique, variegated appearance reminiscent of marble. The absence of aggregate exposure contributes to the floor’s modern appearance, making it a favorite for modern and contemporary residential designs.
This type of polished concrete is especially well-suited for new residential construction, where it is one of the most common installations.
PROS OF CREAM POLISHED CONCRETE
Fast Install Time
Low Price
Natural, Modern Appearance
Well Suited for High-Gloss or Satin Polishing
CONS OF CREAM POLISHED CONCRETE
Can only be Installed on New Concrete Pours
Appearance is Highly Dependent on Pour and Mix Quality
Can Scratch in High-Traffic, Commerical Installations
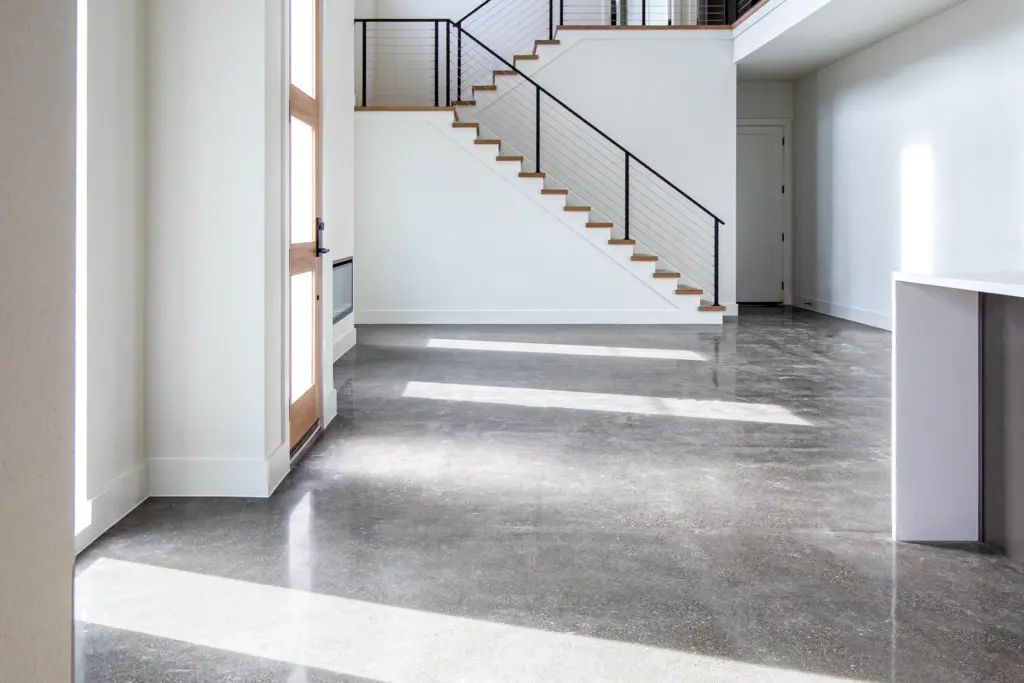
SALT AND PEPPER POLISHED CONCRETE
A salt and pepper polished concrete floor, also known as a Class B finish, is created by lightly grinding the surface of the concrete to reveal the smallest aggregates in the mix. Although frequently specified in new residential construction, the salt and pepper finish is also widespread in commercial and industrial spaces due to its high durability. In residential renovations, where cream-polished concrete is not an option, this finish is a preferred alternative. A salt and pepper finish is generally considered a higher-end or more luxurious option, making it a popular choice for luxury residential construction.
PROS OF SALT AND PEPPER POLISHED CONCRETE
More Durable than Cream-Polished Concrete
Can be Installed in Renovations and New Construction
Well Suited for High-Gloss or Satin Polishing
Can Increase Consistency on Slabs with Low Quality Pours
CONS OF SALT AND PEPPER POLISHED CONCRETE
Longer Install Time
More Expensive than Cream Polished Concrete
May Expose Slab Porosity, Requiring a Grout Coat
Consistent Aggregate Exposure Requires Skill to Achieve
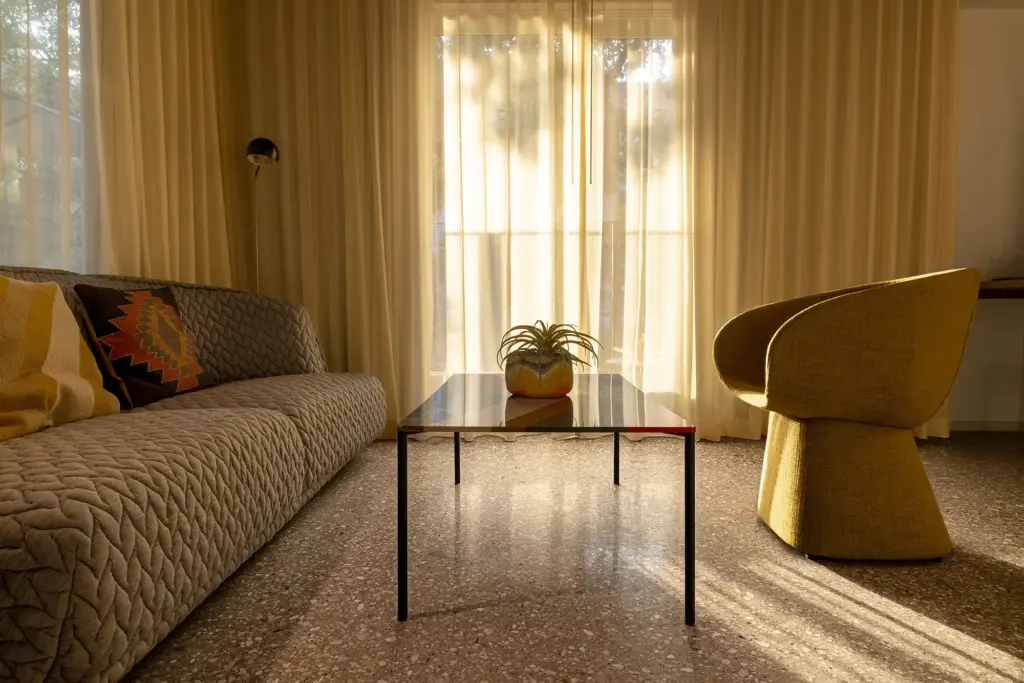
Rock-Cut Polished Concrete
Rock-cut polished concrete floors feature a bold, terrazzo-like appearance achieved by heavily grinding the concrete surface to consistently expose the largest aggregate in the mix. This finish is a popular choice for luxury residential projects, as it provides a unique aesthetic. However, not all concrete slabs are suitable for this technique, as the visual outcome depends on the quality and composition of the concrete slab. To ensure a desirable result, creating samples before committing to a large aggregate project is recommended.
PROS OF Rock-Cut POLISHED CONCRETE
Desirable Appearance
Highest Durability Concrete Floor
Well Suited for High-Gloss or Satin Polishing
Can be Installed in Renovations and New Construction
CONS OF Rock-Cut POLISHED CONCRETE
High Install Cost
Long Install Time
Consistent Aggregate Exposure Requires Skill to Achieve
May Expose Slab Porosity, Requiring a Grout Coat
Other Aesthetic Considerations
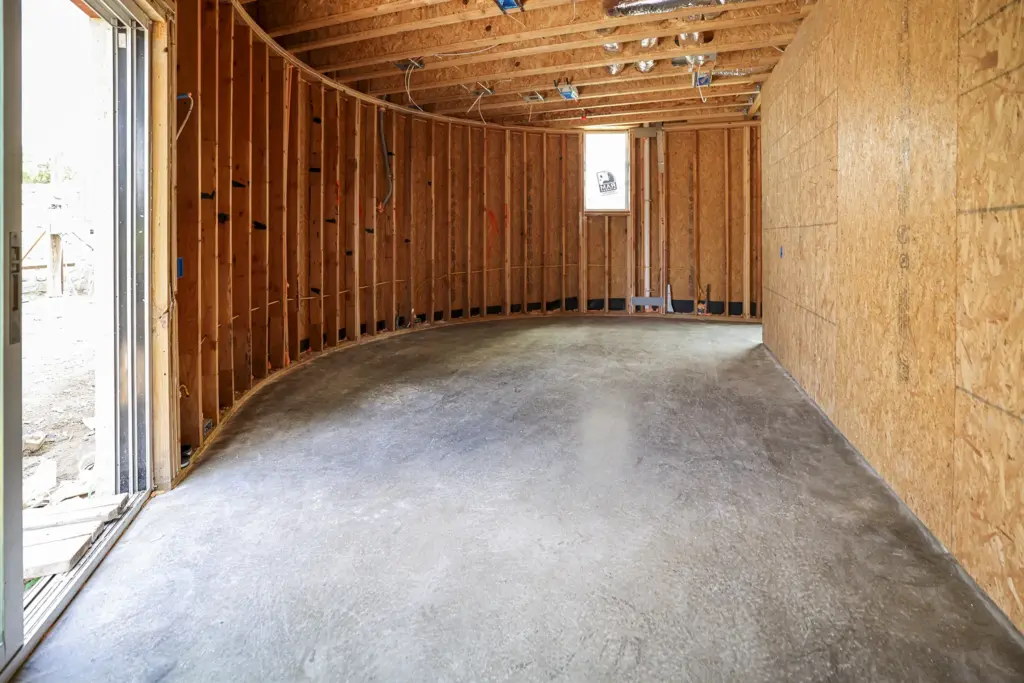
Adding Color To Polished Concrete
Staining Concrete Floors
For new construction, we recommend adding color directly to the concrete mix instead of applying stains or dyes to the surface. This method offers superior durability, consistent color, and a more natural appearance. Stains, by contrast, can fade or discolor in high-traffic areas, requiring ongoing maintenance.
Using Fly Ash for Color and Strength
Concrete color can also be adjusted by modifying additives like fly ash—a coal byproduct that enhances strength and hardness. Standard concrete mixes contain about 5% fly ash, but increasing this proportion deepens the color and hardens the floor. For light-colored polished concrete, skip additives entirely. Check out our guide on how to achieve light gray polished concrete floors for expert tips.
Avoid additives like fly ash or slag for finishes other than cream-polished. These materials can clump, increasing porosity when the top layer is removed during polishing.
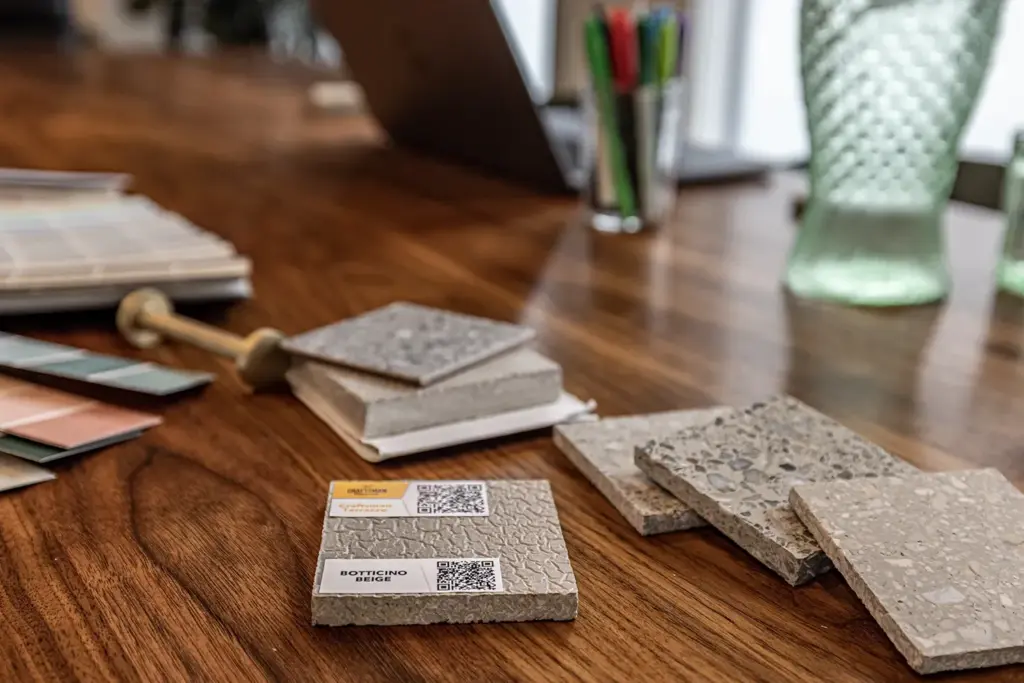
Selecting Aggregates For New Construction
Aggregates (rock and sand) make up 60% to 75% of a typical concrete mix, adding strength and preventing cracking. During pouring and troweling, smaller particles rise to the surface while larger ones settle. Aggregates are sourced from quarries, rivers, oceans, or recycled materials and can be customized for size, shape, and color. This is crucial for finishes where the concrete surface is removed to expose the aggregate for polishing.
For a salt-and-pepper finish, rounded river rock works well. Its smooth edges allow larger stones to sink, leaving only sand and small particles exposed. For a rock-cut finish, jagged-edged rocks stay suspended near the surface, creating a dense, terrazzo-like look.
In many cases, architects or interior designers will help a home or business owner determine what specifications will work best for their goals.
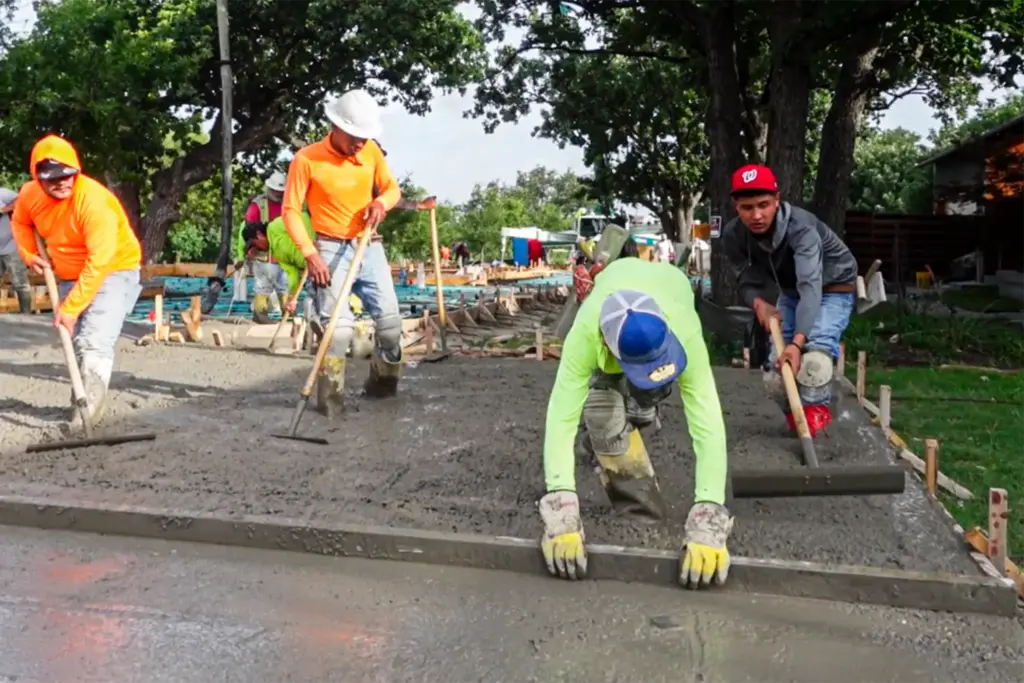
Troweling Technique
For most applications, using float pans under a power trowel creates the flattest possible floor while preserving the cream layer. When finishing a cream-polished floor, avoid hosing water onto the slab—it may help with workability but risks washing away the cream.
To maintain a light-colored finish, avoid over-troweling, as it can darken the surface. For best results, use plastic float pans for two passes, followed by two passes with plastic blades. Minimize the use of steel blades when possible. This method ensures a flat, light-toned finish ideal for polished concrete floors.
Our Clients
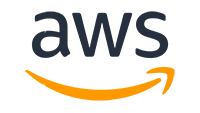
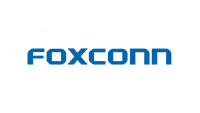
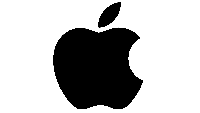
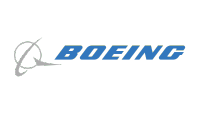
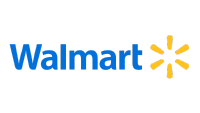
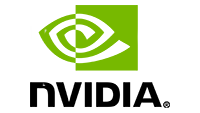
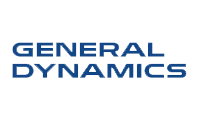
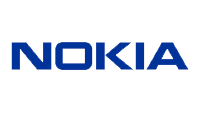
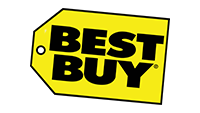
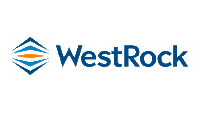
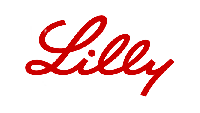
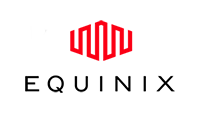
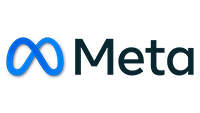
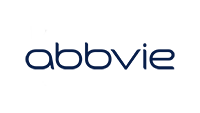
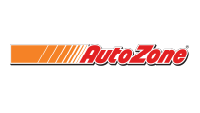
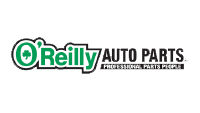
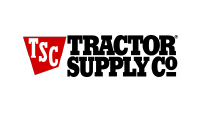
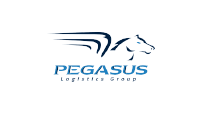
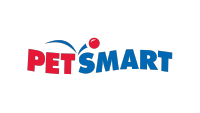
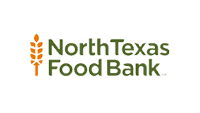
More About Concrete Polishing
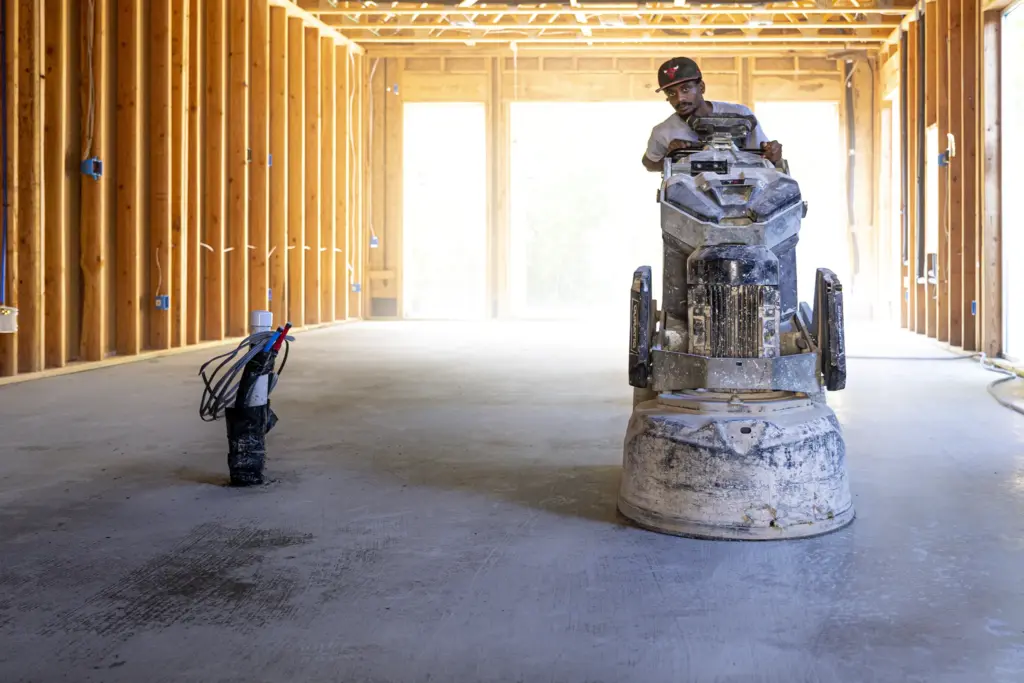
CUTTING
For polished concrete floors with exposed aggregate, the first step is cutting. This process removes the slab’s surface to expose aggregate, with sizes ranging from sand to large rock. Cream-polished floors skip this step, as the surface is not cut before polishing.
Cutting requires aggressive tooling made from diamonds bonded in metal, designed to efficiently grind concrete. A typical cut involves at least three steps, often progressing through 40, 80, and 120 grit tools.
The amount of exposed aggregate is typically specified in architectural plans. The Concrete Polishing Association of America defines exposure levels from A (minimal) to D (maximum). While larger aggregate exposures demand more time and expertise, they deliver stunning, modern finishes unachievable by other methods.
At Craftsman Concrete Floors, we excel in creating these large aggregate finishes, offering polished floors with unparalleled visual impact.
CLASS | EXPOSURE | CUT DEPTH |
A | CREAM | NONE |
B | SALT AND PEPPER | 1/16TH INCH |
C | SMALL ROCK | 1/8TH INCH |
D | LARGE ROCK | 1/4 INCH+ |
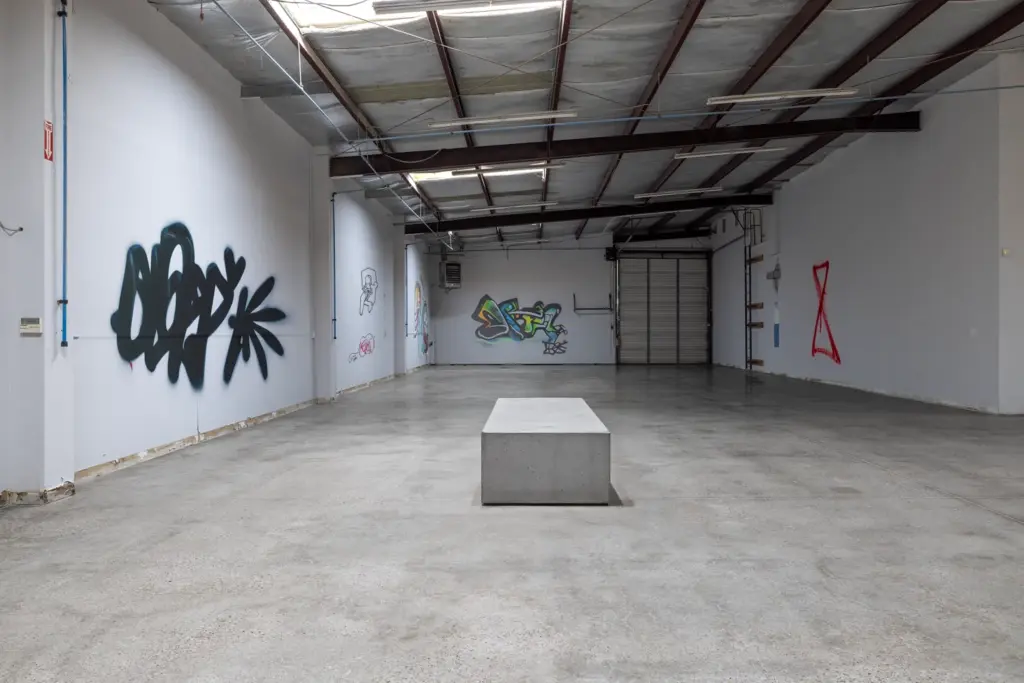
POLISHING
The polishing process gives concrete its reflective finish. Using diamond tooling bonded in resin or plastic, this step removes minimal material while refining the surface. A standard polish involves four steps with 100, 200, 400, and 800 grit tools. For maximum reflectivity, additional passes with 1500 and 3000 grit may be added.
Reflectivity Levels
Polished concrete reflectivity is classified into four levels by the Concrete Polishing Association of America, with Level 4 being the most reflective. Residential floors typically aim for Level 2 – 4 finishes.
LEVEL | GRIT | APPEARANCE |
---|---|---|
1 | 200 | Matte and Non-Reflective |
2 | 400 | Satin – Diffusely Reflects Light. |
3 | 800 | Polished – Reflections can be Identified. |
4 | 1500+ | Highly Polished – Mirror-Like Finish. |
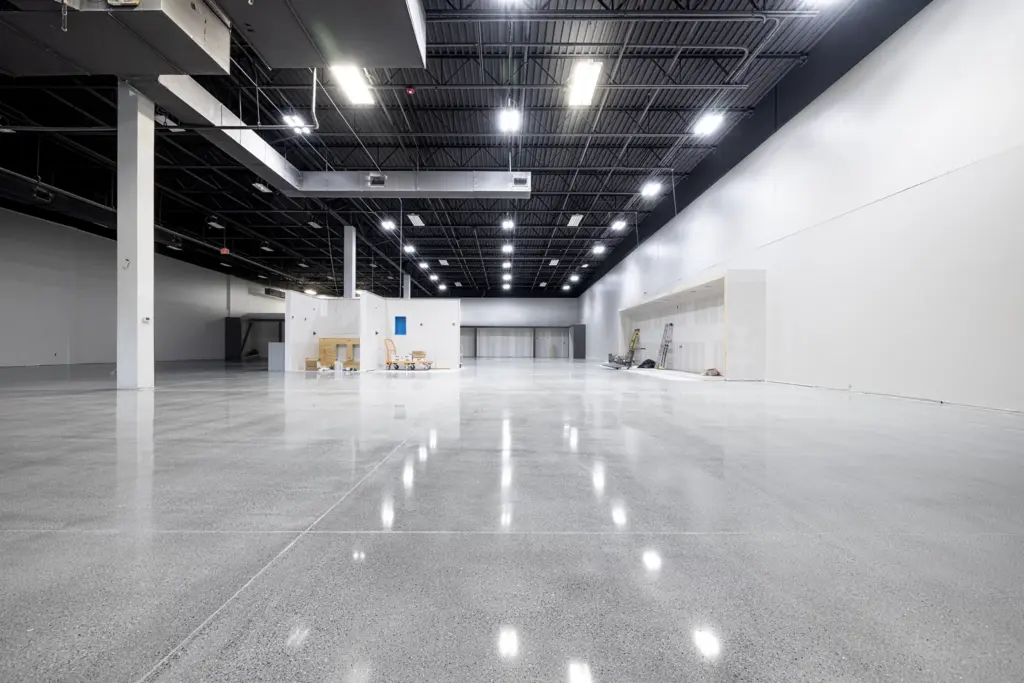
IMAGE CLARITY
A stunning polished concrete floor is about more than just reflectivity. While reflectivity measures how much light bounces off the surface, clarity defines the sharpness of reflected images. Achieving clarity depends on floor flatness, density, and porosity.
Dense, nonporous, and perfectly flat floors create mirror-like reflections without waves or distortion. Properly polished concrete delivers crisp, clear reflections free of haze.
Blog
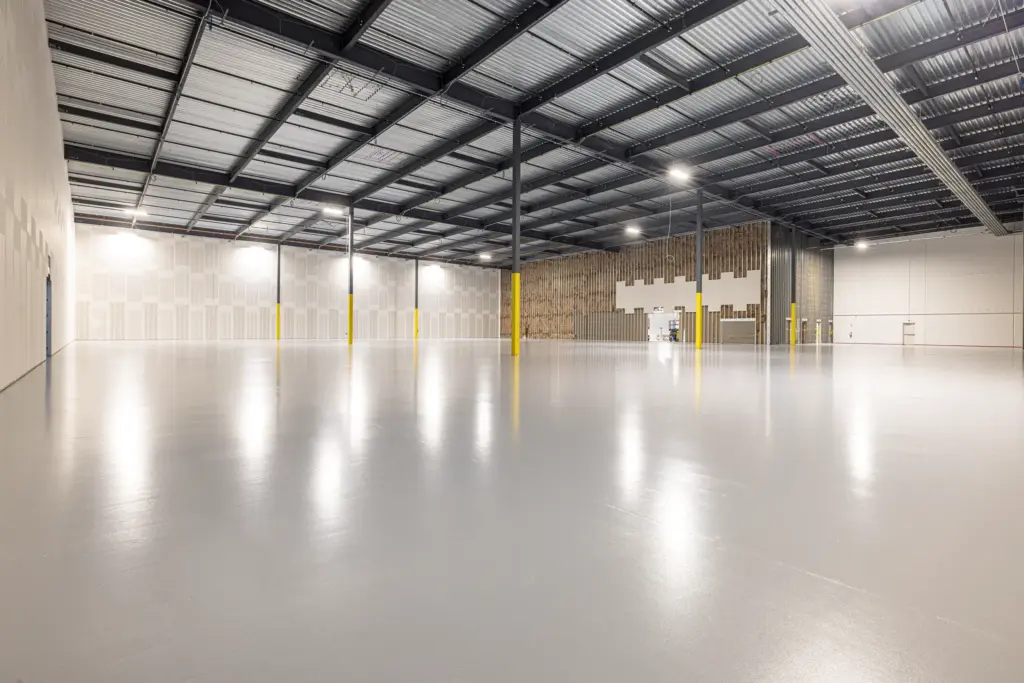
Project Highlight: 34,000 Sq. Ft. ESD Epoxy Installation in Dallas, Texas
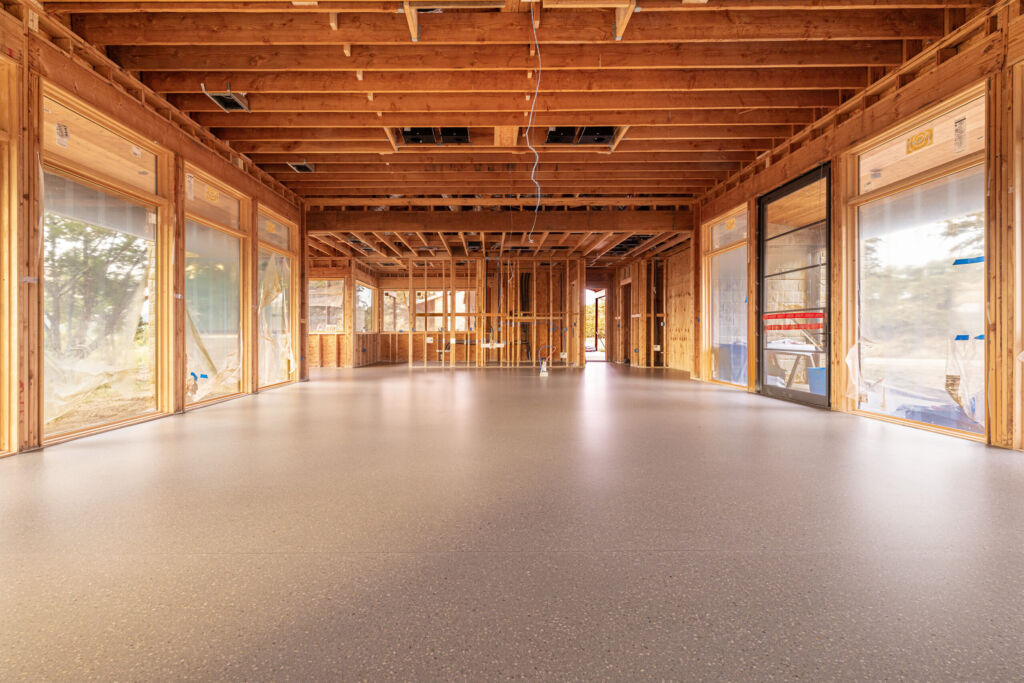
Project Highlight: New Residential Terrazzo Floors in Fort Worth, Texas
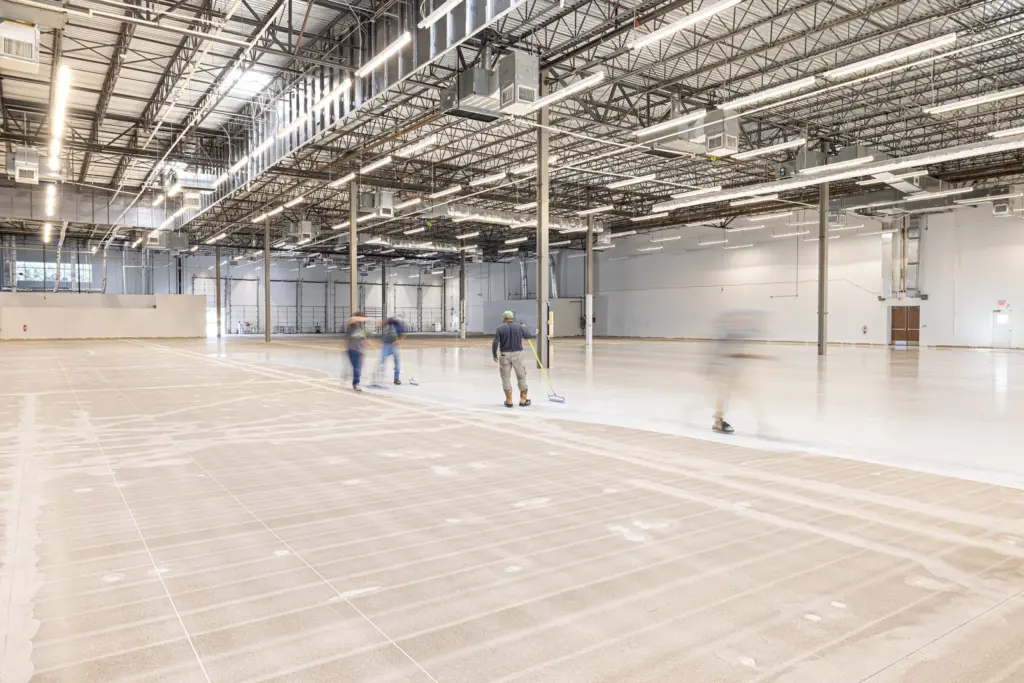